Interview by Dan Gettinger
Every month for the past year or so, new stories have emerged predicting that unmanned aerial vehicles could be used on farms across America. On Aug. 25, the Memphis Commercial Appeal wrote that drones could assist peanut farmers in Georgia to “pinpoint the optimal time to pick peanuts.” A public panel in Ventura, California this week will explore opportunities for drones in agriculture. At the annual Farm Science Review in Madison County, Ohio on Tuesday, farmers got a look at the technology that could change the industry.
More American industries are turning to robots and other automated systems for a variety of reasons. Many predict that drones will herald a new age for agriculture, one that is based on aerial mapping and precision. “Precision agriculture” is a farm management system which utilizes aerial photography and sensors to manage crop variability. For example, the University of Aalborg in Denmark is developing a drone system that can spot weeds by identifying differences in the color of foliage. The popularity of unmanned systems on the ground and in the air has been steadily rising, with the drone being but the latest technology to contribute to this trend in agriculture.
The prediction that ag-drones could occupy a large portion of the domestic market has not occurred in a bubble. The use of robots in agriculture is keeping pace with other industries like textiles. Earlier this summer, the Center for the Study of the Drone interviewed John Fendrick, an owner and manager at Rock Hill Orchard in Montgomery County, located outside of Washington D.C. in Maryland. John recently installed a robotic milking system on the dairy portion of his farm that is made by DeLaval, a Swedish company that specializes in milking equipment.
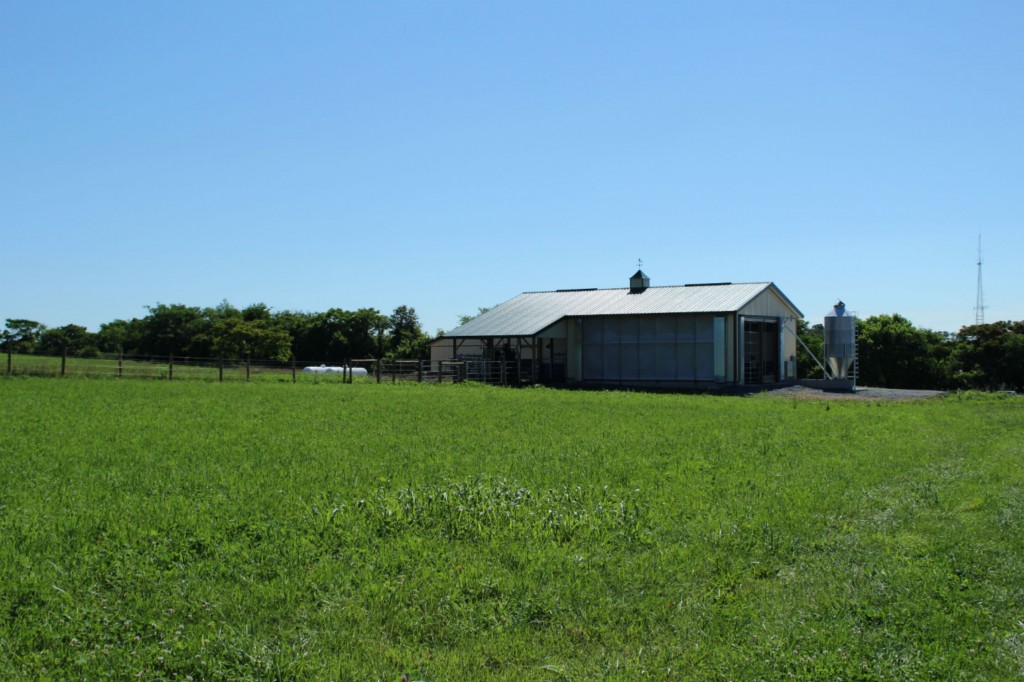
Could you describe what operations you are running on this farm?
We have a 140-acre fruit and vegetable pick-your-own operation with a farm market on site, and then last year, we started putting in a manage-intensive grazing operation on the back 60 acres. Manage-intensive grazing is where the cows move from pasture to pasture every day, and then the grass gets about a 30-day rest so that what happens is that the cows are always getting very high nutritional grass.
Because of that, we actually get what I consider to be a reasonably high amount of milk. When the cows move from a traditional farm where they are being fed silage and grains to the pasture, they lose about a third of their production. Here they are getting 99 percent of their nutrition off of grass. So I lost some of their production but I have virtually no cost in feed.
When we bought this farm a few years ago, the long-term plan was to put a milking parlor here, because we already had a herd, and we wanted to basically be able to process our own milk and cheese and sell it locally. We like to buy local and knowing where our products come from. We started planning for a traditional milking parlor operation a year ago. It is basically having the cows on the two sides with a depressed area in the middle where you can walk. It’s a very manual operation. Twice a day you have to have someone, whether it’s us or a hired person, to come and milk the cows every day. No days off, no nothing.
A year ago, we went on a tour, and we actually had seen a single robot at a farm and thought this was kind of interesting. Typically, robots are put in larger operations. It’s very rare that you see one robot.
What do you mean by larger operations?
Each robot serves about 60-65 cows. A typical operation is somewhere in the hundred to 300 cow operation. The one with 24 robots mentioned earlier actually milks a couple thousand cows. The more typical has two to eight robots; very rarely do you have somebody with a single robot.
But a single robot actually works out really well. When we went to visit this guy with the single robot, we met him and he gave a tour. He was talking about the lifestyle change. That is the big thing with this, it’s the lifestyle change. No longer are you tied to being there exactly for about two hours per milking, twice or sometimes three times a day. Say it’s twice a day, between 6 and 8 a.m. and 4 and 6 p.m., you have to be there every day, the cows will be waiting for you. If you’re half an hour late, they’ve been waiting half an hour. He talked about the lifestyle and he had an off-farm job. And then the lightbulb sort of clicked, and we thought maybe we should do this and that’s where the whole idea of the robot started for us.
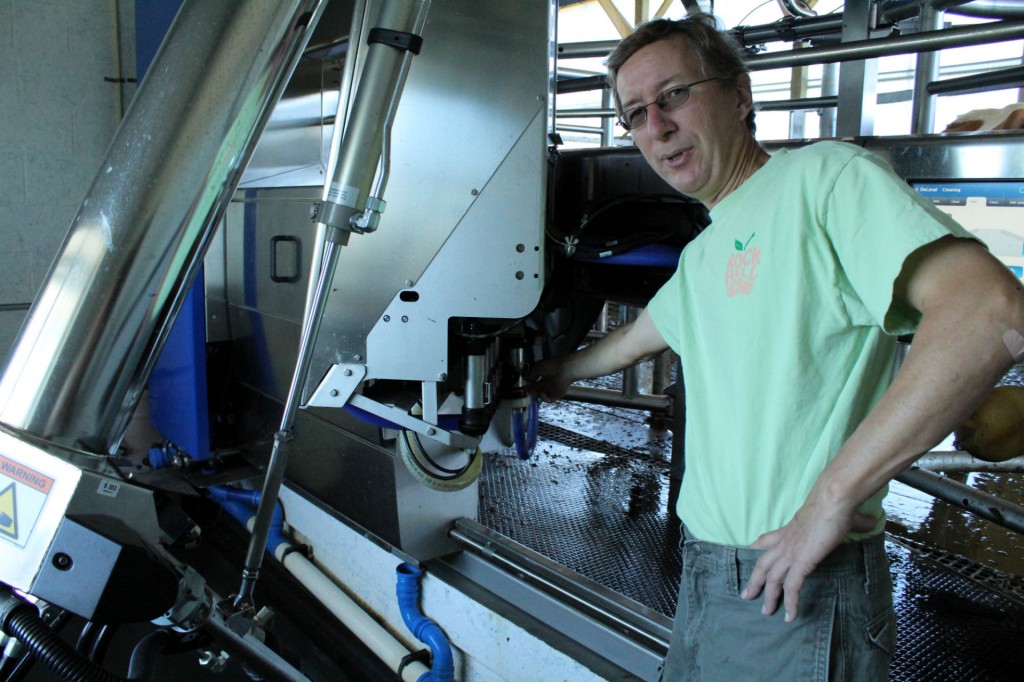
How does the robot work?
The cows come in from the pasture by themselves. The way we have the grazing set up, the cows are in one pasture in the morning and another in the evening but every time the cows switch pastures, they come into the dairy. If they have milking permission, which is every six hours, they are let into the parlor. Each cow has an RFID (radio-frequency identification) in its ear with a unique number. Essentially, the way it works is that they come into the holding area, and for them to be let back, out they go through what’s called a ‘smart-gate.’ The smart gate can either send them to pasture A, pasture B or back into the milking area. At this point, the cows know that if they get stopped, they just turn right back around and head back to the parlor.
The cows are trained. The only thing that we do is show them how to get into the space used by the robot; everything else they figure out for themselves. They come in completely by themselves, though sometimes we have to head out to fields to check on one if it turns ‘red’ in the computer. A cow might go up to 18 hours, but they always come in. If you’re willing to let your cows go a little bit longer once in a while, it’s ok. As long as a cow doesn’t go too long in between milkings.
We get around 2.2 or 2.3 milkings per day, which means they are milking about ten hours apart on most days. If they come in late, chances are the next day they will come in and make up for it by coming in three times. It’s a rotating thing.
They come in off pasture, stand by the robot in a pen and then just walk in. There is an automatic gate so if a cow’s out, they walk right into the robot. They are fed a little bit of food, just to tell them, ‘hey, this is a good place.’ This is a special mix made to give them the minerals they need to be able to produce better. On average, they eat around six pounds of this milk per day which, in a milking herd, six pounds is very little. It sounds like a lot, but in terms of what these cows are eating, it’s basically nothing. Conceptually, it’s like the whip cream on top of the ice cream.
Our robot is called a DeLaval VMS. The way the machine works, it sprays the teat with iodine and cleans each one by spraying a warm mixture. It’s sort of like a whirlpool bath. Then it dries the teat by a vacuum process which also does a pre-strip of the cow. It goes through all four quarters, and then the robotic arm goes and attaches and starts milking. The computer senses the flow rate of the milk coming out so when the flow goes low, it stops milking.
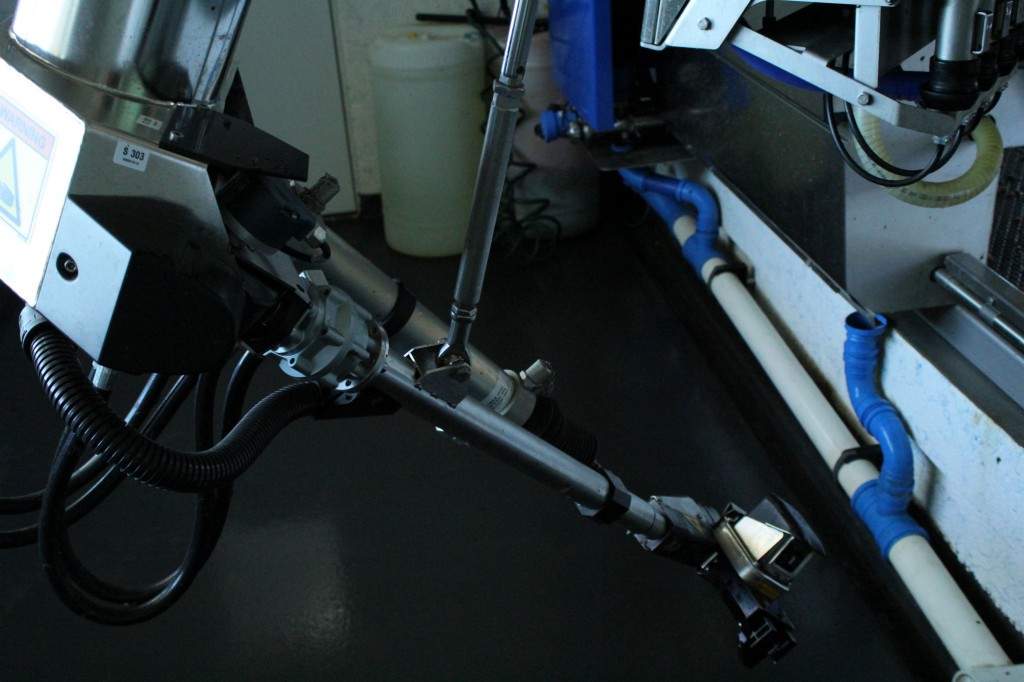
On some of these animals, there is a 10-pound difference of milk depending on the quarters. In a traditional dairy, all four quarters are milked at the same time, which sometimes leaves milk in one of the quarters. If you leave milk in the quarter, you’re more likely to get mastitis disease. Each quarter is different, so this is sort of milking is based upon what each quarter does. Often dairy farmers will know, ‘well, this quarter I have to milk more than the others;’ and that works if it is the same person milking every day. But if you have help, they might not milk the same way.
With the robot, every cow gets milked according to their needs. In this case, it will sometimes milk in one quarter for a longer period of time. It’s more sensitive and is milking more for what the cow needs.
Part of what a lot of what a dairy does is routine. You want it to work the same way every day. In dairies where there is a lot of bacteria problems, or problems with the milk, it’s because a different person’s milking or there’s a problem with the pulsation; there is something different. Here everything is done the same way. We might have some of the same issues, like if the compressor goes bad or something, but for the most part, everything is done the same way. And if a cow has a light quarter, we can set the machine to just milk three quarters.
We’re not an organic dairy. If a cow has mastitis, we will treat the quarter. If a cow is sick, the cow might get penicillin. We enter all of this into the computer so that the whole system knows that this medicine has, for example, a five day withdrawal time. That means that, automatically, for five days that cow’s milk will go down the drain. You can set the system up to divert the milk to different ends depending on that particular cow. Say, for example, the cow just gave birth. The milk from that cow, which is full of colustrum, will be diverted to a pail for the calf. In a traditional dairy, when a cow is treated, a colored band will go on it’s foot and people working there have to know what those bands mean. We don’t do any of that. This helps our operation because we’re not here all the time. For us, this is not the only operation we do. We’re not doing just the dairy as a full time job.
Our system will tell us where our cows are, but once it a while it makes a mistake because two cows go through the gate at the same time, which happens sometimes. A drone might be useful because we could send it up and have it search for cows based on their ear tag radio chip.
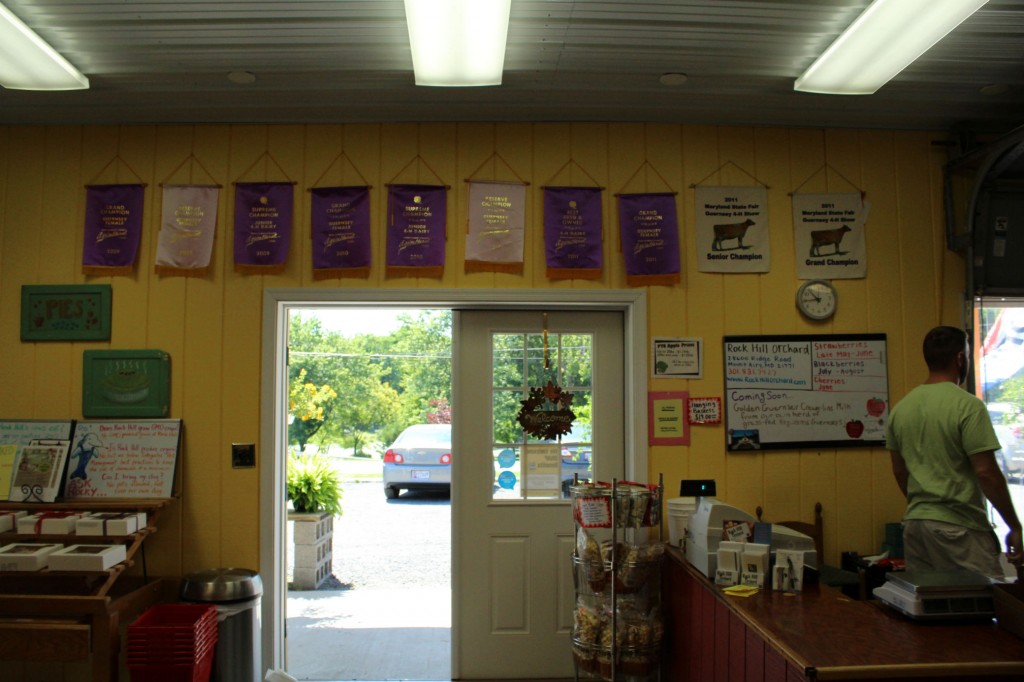
So was it the change in lifestyle that appealed to you?
It was the lifestyle change since we have a whole other working farm with fruit and vegetables. Most people say an orchard is a full time business. We have an orchard, a farm market, vegetables, and now we have an entire dairy. Effectively, on this farm, we probably have somewhere between two and three full-time jobs that we already need to worry about before we even put the dairy in.
I think most people in the orchard business, while they applaud us, also probably think we are a little crazy. Typically, having an orchard with a pick-your-own, it’s a big endeavor.
We worked with a local vendor and the builder. It turns out we are first all-pasture robotic dairy operation in North America. There are other pasture-based operations where the cows are out in the pasture for six months and inside for six months, but our cows are in pasture all months of the year. We will dry off a portion of them during the winter, but we will still have some milking all winter. Part of the reason for this is that you can’t ever let the robot freeze. So if we’re going to have to heat the robot and keep it running anyway, we might as well use it. The other part is that we also do processing of milk and cheese and once you build up a market for your milk, you don’t want to tell them that it’s only available half the year. I’d rather process it at a lower volume during the winter than lose the customers.
Is this a popular system with farmers?
It has to do with cost. Probably very few grazing operations look at it because, although grazing is better for the cows, it’s also a lifestyle choice. What happens with grazing, and I’m going to generalize, is that people who graze give up milk output but they are putting less into it. They are getting more time with their families because the cows are doing to work for themselves by feeding in the pastures.
The robots are reasonably popular, though a lot of traditional dairymen are leery of them. It’s different, and it costs money. Luckily for us, ours was financed by the manufacturer so it wasn’t too bad because they had good financing terms. The bank we talked to, even though they only finance farmers, didn’t want to finance this system. From our point of view, the manufacturer’s financing is beneficial for us because they only take a lean on the equipment. Most of the time, when you put up farm buildings there’s a lean on the farm. This time, it’s on the equipment itself which keeps its value very well. For this robot, the technology hasn’t changed too much conceptually about how it works.
The farms looking at this system are probably in the 150-400 cow range. For us, we think it’s a great thing but most farmers at the 50-100 cow range don’t have the ability to borrow the money to invest in this. But they are the ones who can gain the most. Typically, they are a one person or family operation with limited help and this is where this system really comes in. We would pay for this in a few years just from labor savings alone.
If you take a small farm – a husband and wife and maybe a child- at certain times of the year they are doing other tasks as well like making hay and cleaning up in addition to running the parlor. So they are the ones who could benefit the most but they don’t have the capital or the ability to raise capital to put one of these in. So it’s typically the larger operations that have this system.
In Montgomery County, our county, we’re the first all-new dairy facility in sixty years. When I talk to people, at first they say, ‘that just can’t be.’ But it really it’s been since the 50’s that a new investment in dairy was made around here.
Are you pleased with your investment?
Oh yeah, definitely. I’m able to go out in the evenings, and I can go to my day job and the system calls me whenever there is a problem. And most of the diagnostics is done remotely either by phone or by calling up the support people who can just dial in and remotely fix it.
John Fendrick manages Rock Hill Orchard together with his wife, Mary Fendrick. John is the President of Woodbourne Solutions.
Photos by Dan Gettinger.